Publication
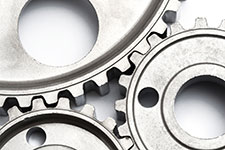
Managing supply chain risk – moving beyond anti-corruption compliance
Global | Publication | February 2016
Content
- Ways your supply chain can impact your brand
- Quality and safety
- Bribery and corruption
- Human rights impacts, including worker safety
- Environmental impacts
- How to manage supply chain risk
- Contractual language
- Explicit commitment to human rights, anti-bribery and sustainability at pre-contract stage
- Supplier due diligence
- Audit, certifications, training
Ways your supply chain can impact your brand
- In Europe in 2013, horse meat was found in a number of products labelled as ‘meat’, ‘pork’ and ‘beef’. The scandal revealed a major breakdown with traceability in the food supply chain and fraud. Major retailers acted to cease relationships with the brands that had supplied horse meat. Sales of frozen hamburgers fell by 43 per cent in the EU over the coming months.
- A corporation engaged intermediaries in a variety of markets to introduce it to potential government purchasers. Allegations have been made of systemic bribery by these intermediaries. The corporation is being prosecuted, as are its officeholders. It has been excluded from bidding on new projects in some jurisdictions pending the outcome of the prosecution.
- An NGO has recently released a score card for numerous participants in the Australian fashion industry. All major newspapers around Australia report on the human rights performance of the companies reviewed.
- In 2014, Oxfam Australia released a report alleging that Australian banks had financed corporations involved in illegal logging, forced evictions, inadequate compensation, food shortages and child labour. In response to the report, each of the banks agreed to work with Oxfam to look into the issues raised.
More than ever, businesses are using global supply chains to remain competitive. Often this involves businesses transferring parts of their supply chains to developing nations to benefit from reduced costs, particularly labour costs. At the same time as supply chains are becoming global and unwieldy, the community, regulators and NGOs are holding businesses accountable for all parts of their supply chain. This poses real challenges for businesses, whose reputations are now reliant upon the conduct of disparate suppliers, over whom they have traditionally sought to have little control.
What follows is a summary of some of the different ways that a business’s supply chain can impact its reputation. In short, supply chain management has become an essential element in minimising a fundamental brand risk. We finish up with some thoughts about managing that risk.
Quality and safety
As a critical threshold issue, a business needs to be able to rely upon a supplier to provide products or services of a consistent quality and safety.
The recall of frozen berries sourced from China earlier this year demonstrated the supply chain risk for businesses in the food and retail sector, even in circumstances where it is denied that there was a link between the berries and the hepatitis A outbreak. Supply chain risk is also substantial in the construction and extractive industries. These industries engage numerous contractors and subcontractors on projects, all of which have the ability to impact upon the reputation of the head contractor. A major concern for many mining companies with projects in developing countries can be the behaviour of the private security firms engaged to protect the mine sites.
One substandard element of a supply chain can cause substantial reputational damage. Although supplier selection is often focussed on this issue, processes need to be adopted to routinely review the performance of suppliers.
Bribery and corruption
Supply chains can cause extreme bribery and corruption risk. There are a number of core bribery and corruption (BAC) supply chain risks:
- a supplier may pay or accept a bribe in connection with their role in the supply chain
- in some markets, a supplier of services, such as an intermediary, might be a foreign official creating a high BAC risk
- a supplier may pay a bribe to an employee of a business to win a mandate, costing the business at least the amount of the bribe (which presumably would otherwise have come off the negotiated price)
- employees may use suppliers to pay bribes in relation to a business, or suppliers may be asked to overinvoice to create a ‘slush fund’ that can be used for bribes
- a supplier may have paid bribes on behalf of another client and be investigated. Commonly regulators will expand their investigation into all businesses utilising the services of that supplier.
The BAC legal and reputational risk arising from supply chains can keep you awake at night if you do not have a robust compliance program. Such has been the impact of bribery allegations upon a brand that companies have been known to rebrand following bribery allegations.
Human rights impacts, including worker safety
The last few years have seen a global trend of businesses being held responsible, at least by NGOs and consumers, for the human rights impacts of their entire supply chain.
The Guiding Principles on Business and Human Rights were unanimously adopted by the United Nations in 2011. They have produced an expectation about how businesses will manage their impact on human rights. Human rights due diligence is a core element of the Guiding Principles. The Principles provide that prudent corporations ought to identify and assess actual and potential human rights impacts throughout their entire supply chain. Businesses should then seek to prevent or mitigate those impacts, using whatever leverage is available to them where that negative impact arises from part of their supply chain. The Guiding Principles have become a new global norm.
We are seeing increasing activism in relation to human rights. In Australia, NGOs and the media have recently focussed upon supply chains in industries such as agriculture and food, timber production, mining, fashion and banking. Brand protection requires businesses to be ready for questions about the human rights impact of their entire supply chain, so you should not to wait until the questions are asked before you consider their impact upon human rights.
Environmental impacts
Popular opinion is also holding businesses accountable for the environmental impacts of their supply chain. Manufacturing, extractive industries and agriculture all have the potential to cause a significant detrimental environmental impact.
Environmental issues are increasingly being viewed as overlapping with human rights. For example water pollution may impact upon the right to life if the pollution prevents local access to clean water. Environmental issues can also impact upon product quality in some industries such as agribusiness, expanding the reputational risk substantially.
Various Australian businesses have introduced Environment policies that extend to supplier selection and continuous review. Most Australian banks have adopted the Equator Principles, which provide a risk management framework in relation to their projects, as well as in connection with their internal environmental and social policies. All of these measures reflect an awareness of the potential impact of environmental impacts upon brand.
How to manage supply chain risk
Businesses seeking to manage their supply chain risk need to start with a review of their relevant policies and procedures. This should include a gap analysis that will identify the areas for improvement and an audit which tests the effectiveness of existing processes. Areas of focus when considering supply chain risk are highlighted below.
Contractual language
Although inserting appropriate contractual terms requiring suppliers to manage the risks described above is important, it does not provide a complete answer. Businesses cannot rely upon these contractual obligations for legal or brand protection. Other strategies to manage supply chain risk include those outlined in the sections below.
Explicit commitment to human rights, anti-bribery and sustainability at pre-contract stage
Businesses should make their commitment to human rights, environmental sustainability and zero tolerance for bribery explicit, both in their advertising and in requests for tender. Requests for tenders should state that tenderers are expected to similarly commit to these principles and will need to demonstrate that they are not aware of any breach. This commitment ought to be included in the express selection criteria. Draft contracts presented to suppliers should enshrine these principles.
Supplier due diligence
The most critical element of a supply chain management program is the selection of suppliers. Businesses need to conduct due diligence into their supply chains. This is the primary means by which businesses can control all of the brand risks described in this paper.
The due diligence conducted needs to be responsive to risk. A pragmatic supplier due diligence program ought be developed that focuses resources on high risk suppliers. There is no substitute for visiting suppliers as part of the supplier due diligence.
Supplier due diligence may involve the following steps (and more):
- establish who your suppliers are, their location and what it is that they do for their remuneration (consider whether it is a reasonable fee for the service provided). This will include running appropriate company and other searches to make sure that you know who you are working with. This is easier in some jurisdictions than others
- establish that there is no unauthorised subcontracting by your suppliers and check that you are aware of each of the elements of their supply chain (as it pertains to their supply of services to your business)
- review suppliers’ processes to make sure you are confident that each supplier can ensure product or service quality and safety
- ensure that appropriate policies, procedures and whistleblowing processes are in place and, if not, collaborate with suppliers to develop them
- review the work conditions and wages paid to staff, ensure that there are no child labour and all employees are there of their own free will and are not grossly underpaid
- consider whether there is any potential environmental impact of the supplier’s business
- ask to see suppliers’ financial records to confirm that they are an accurate reflection of their operations.
Audit, certifications, training
Finally, there are a few other ways of managing the risk posed by existing suppliers. Consider the inclusion of a right to audit in supplier agreements to permit ongoing assessment of risk (and exercise that right!) Adopting a regular program of testing and auditing could have assisted in the horse meat scandal in 2013.
Introduce regular certifications for all suppliers in relation to BAC and other risks. External certifications can be useful to provide peace of mind. At the very least, this demonstrates that the issue remains front of mind for your business.
Consider rolling out training to suppliers as well as your own staff. Hopefully this will stop your suppliers engaging in conduct that can impact adversely upon your brand.
Recent publications
Publication
Real Estate Focus - December 2024
December has been a very busy month, with a flurry of new government policies and consultations.

Publication
Essential Corporate News – Week ending 20 December 2024
On 13 December 2024 the Financial Conduct Authority (FCA) published Primary Market Bulletin 53 (PMB 53) which includes confirmation of the final form of two new, and one amended, sponsor-related technical notes previously consulted on in PMB 50, and a consultation on various proposed changes to the technical and procedural notes in the FCA’s knowledge base.
Subscribe and stay up to date with the latest legal news, information and events . . .